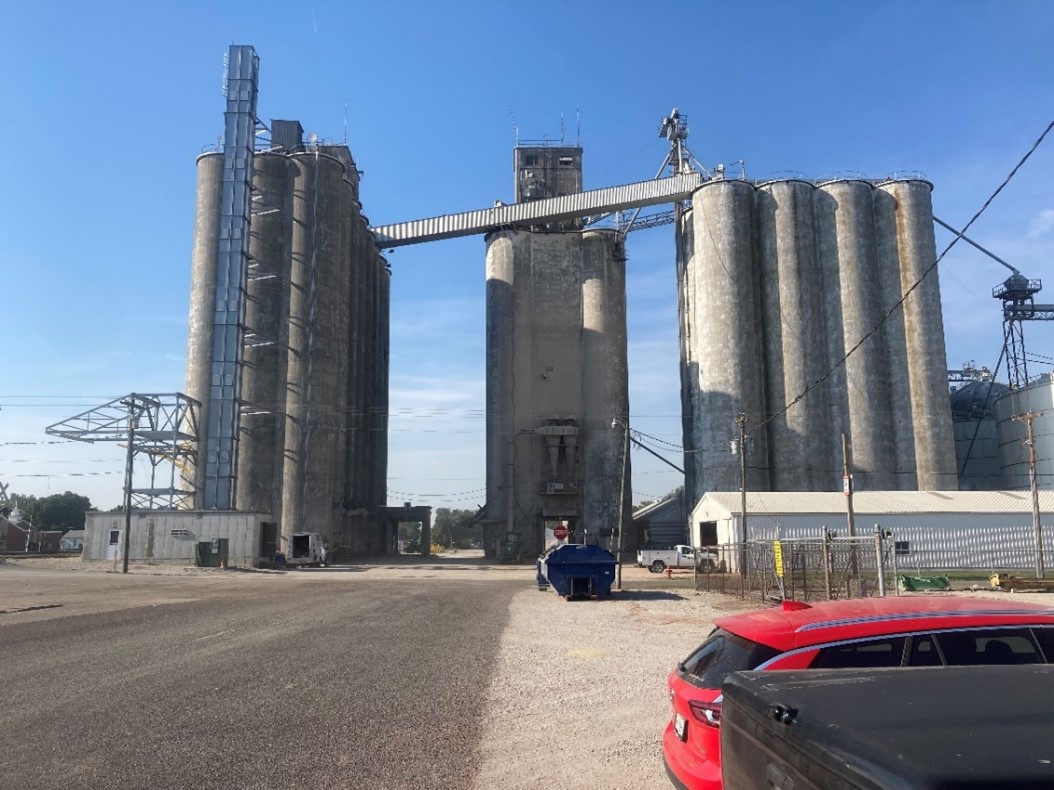
Project Profile: New Automation & Monitoring, Eliminate Labor Costs & Reduce Errors for this Grain Elevator – Central Il
This customer project entailed the addition of extensive process automation and monitoring for the end user for one of their grain storage complexes at the site. This grain elevator customer wanted two operator stations to control everything in the process.
The Process:
The existing process was manual, with grain operators having to open hand valves and physically inspect the grain bin levels.
Based on the scope of automation required, this project required extensive planning. The automation team needed to know I/O counts, voltages, motor sizes, feedback type, etc. In the beginning, there was a moderate amount of uncertainty about how some of the equipment previously purchased would integrate into the control system they were proposing. After the design process, it was discovered that all the gates would have 0-10V feedback rather than 4-20mA. While the analog card would accommodate this, we needed to add a 10V power supply to the system. During startup, additional equipment unknown initially needed to be added to the system. The flexibility of the programming software used by the team enabled changes to the system to be very efficient once everything was identified.
The Solution:
Our proposed solution was a complete Modicon M580 programmable automation control (PAC) system.
The system included an unmanaged Ethernet switch that connected the PAC to five variable frequency drives controlling conveyors (two of them were configured in a server/client architecture), two networks of radar sensors monitoring bin levels, and a hazard monitoring system for specified equipment.
All networked equipment was to be operated via communications rather than digital I/O. The system also included interposing relays for controlling gate motors, starters, and other equipment. For the human/machine interface, Machine Scada Expert was specified. Dashboard screens were to be created to start and stop the equipment, monitor the bin levels, and display the contents of each bin.
The controller would also interlock certain parts of the system in order to prevent accidental spillage of grain, overloading of conveyors and elevators, etc. This included an automatic pause and resume feature for the gates which release grain from the bins. Extensive alarming would also be provided for troubleshooting the system. Certain alarms initiated by the hazard monitoring system would also shut down the equipment. The system also featured a Phoenix Contact mGuard networking device to add the ability to do remote troubleshooting.
The solution was presented through a written proposal. And as the system was developed, there were additional meetings with the electrical contractor and the end user at the site.
The Results:
Several advantages to having an automated system like this over a manual system:
- The ROI comes from things like time savings from operators not having to make estimates physically look in bins to determine the grain levels.
- Also, interlocking the equipment can prevent wasted labor costs from cleaning up accidental spills and jams which can happen without it.
- Interlocking also prevents mistakes and equipment damage to that which has to be started and shut down in a certain sequence.
- The two terminals allow most of the information about what is happening at the site to be gathered in those places.
- In a complex this big, having the information consolidated saves a lot of time.
- With the alarming systems provided, time troubleshooting the system can be greatly reduced. The remote access module from Phoneix is a big saving because it aids in troubleshooting. An engineer can monitor the system from anywhere with an internet connection.
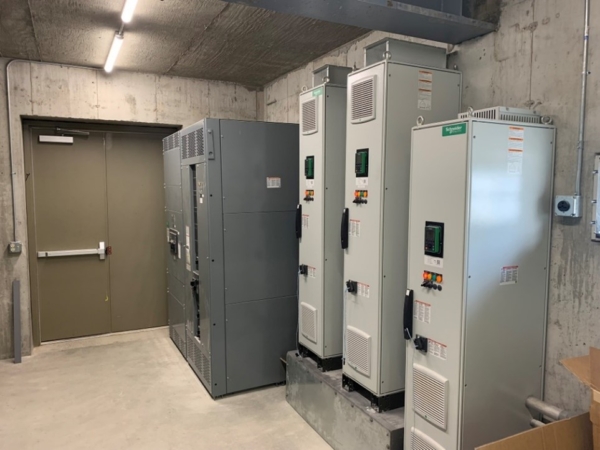
Image 1: Altivar drives in new electrical room.
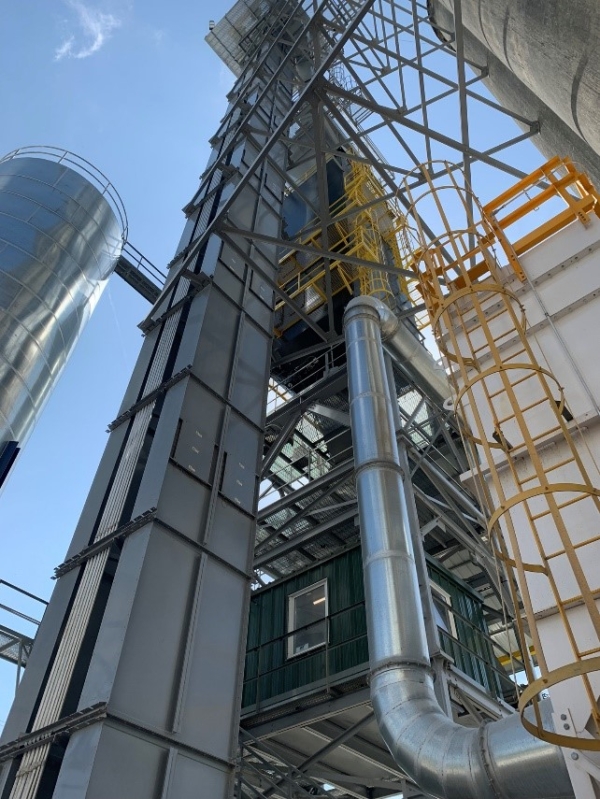
Image 2: New elevator driven by two Altivar 930’s in client/server configuration. The motors are on opposite ends of the shaft driving the bucket elevator and are 200 HP each. The picture does not do the size of this elevator justice. It is huge. The elevated control room at the bottom of the picture houses one of the SCADA control stations. It is at a level where the tops of the rail cars being filled or emptied can be monitored.
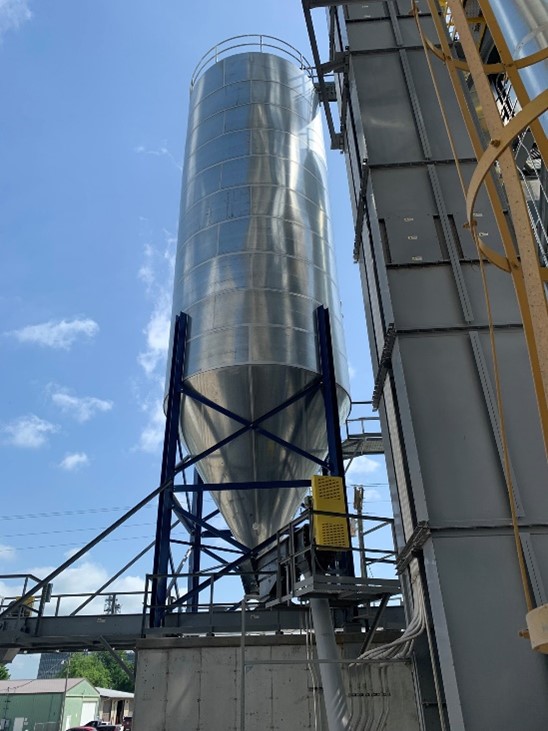
Image 3: This is another view of the new elevator as well as the new fines bins on top of the electrical room shown in a previous picture.
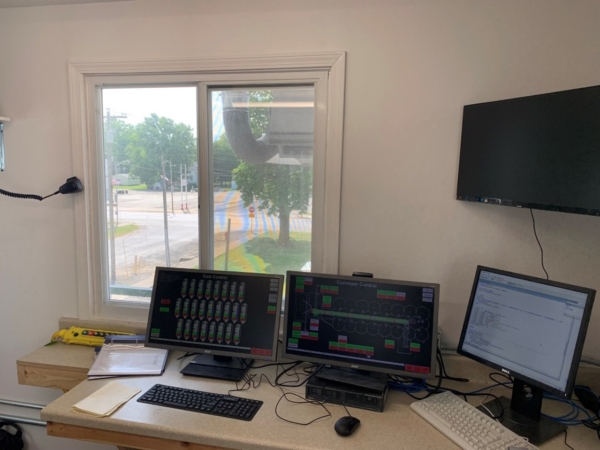
Image 4: This is a view from the elevated control room showing the dual monitor setup displaying the SCADA interface.
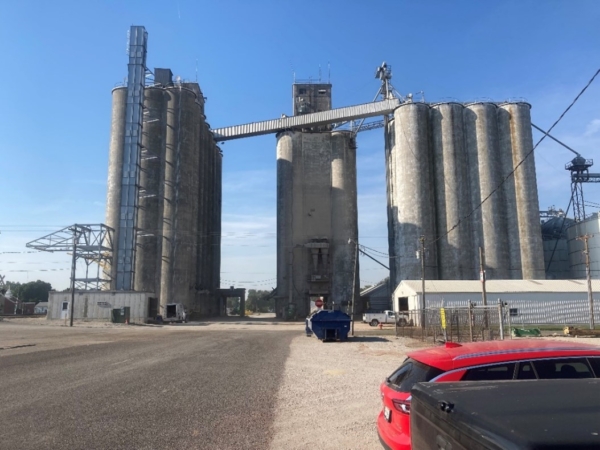
Image 5: This is the site under construction showing the new electrical room, elevator, and framing for equipment to the left of the picture.
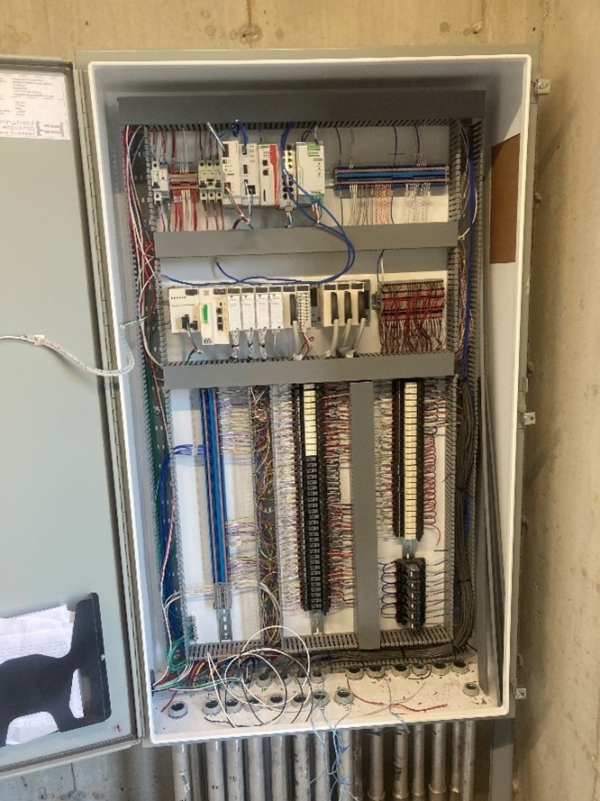
Image 6: This is the main control panel during installation at the site.

Image 7: This is a second panel with drives, starters, etc.
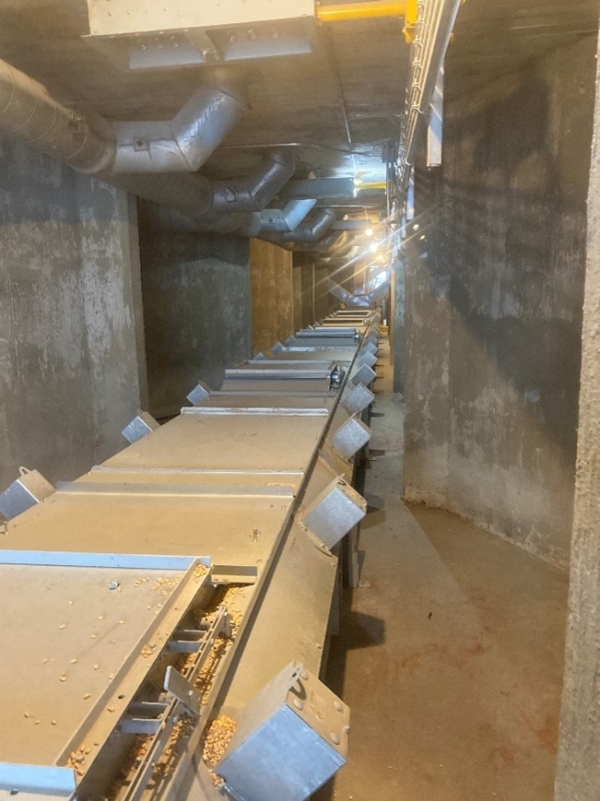
Image 8: This is a view under the complex showing the bottom belt conveyor which carries grain from the discharge gates at the bottom of the bins.
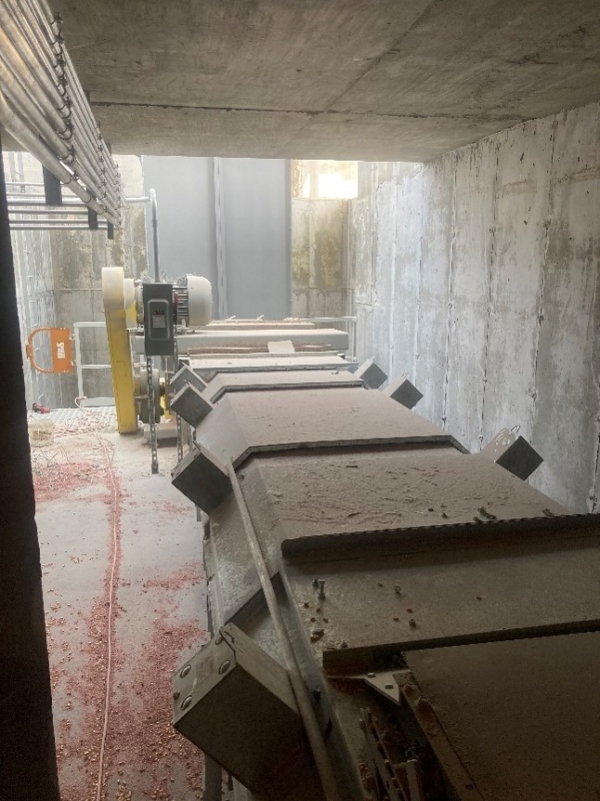
Image 9: This shows the lower level where the bottom conveyor meets the massive new bucket elevator.
At Springfield Electric, we understand the importance of having customized solutions to fit your operation. With our Control Services our experts can help you design a control solution that fits your needs, and we can build it to the exact specifications. Our Experts will be there from conception to implementation, and help educate your team on everything you will need going forward.